Why Are Golf Balls Made of Rubber?
At the core of every modern golf ball is some amount of high-quality rubber material. But why has this become the standard? Why use rubber over other potential compounds for manufacturing golf balls?
In this article, we’ll examine the specific benefits rubber imparts that have made it an indispensable material for optimizing golf ball performance.
We’ll look at the history and evolution of rubber use in balls. We’ll also see how manufacturers leverage various rubber formulations to fine-tune feel, spin rates, and durability.
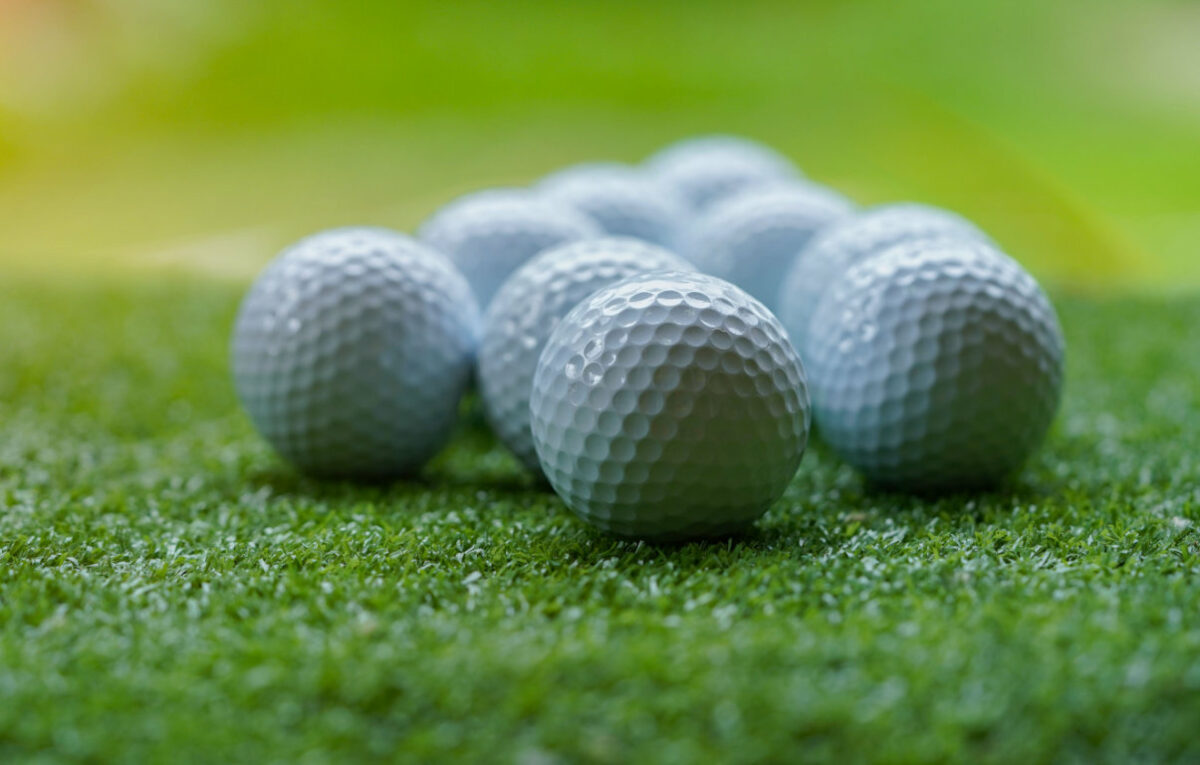
Brief History of Rubber Golf Balls
Gutta-percha, a natural rubber, revolutionized golf balls when it was introduced in the mid-19th century. Prior to that, golf balls consisted of hardwoods like beech and boxwood.
The new gutta percha balls offered golfers:
- Increased durability with the rubber material
- Enhanced playability and consistency
These advantages fueled the mass adoption of the gutta ball, making rubber a standard in golf ball production going forward.
In the 20th century, innovations like wound rubber cores and Surlyn synthetic rubber- covers advanced ball designs even further.
Rubber science gave golfers better-performing, more durable balls.
Key Benefits of Rubber in Modern Golf Balls
There are several unique advantages rubber imparts to golf ball performance:
Resilience – Rubber’s elasticity provides excellent shock absorption and kinetic energy return at impact for speed.
Feel – Advanced rubber compounds dial in a soft, responsive feel and feedback desired by golfers.
Control – Formulations are tailored to impart spin on command for shots around the green.
Durability – Rubber withstands compression forces and abuses far better than plastic or wood.
Distance – Stretching and flexing of rubber cores and layers boost ball speeds.
Thanks to these properties, rubber remains the material of choice for maximizing golf ball functionality.
Rubber Components in Modern Golf Balls
While rubber is critical throughout, the core is most responsible for delivering key performance benefits:
- Solid Rubber Core – Provides optimal resilience and speed in 2-piece distance balls.
- Liquid-Filled Rubber Core – Low compression liquid core wrapped in rubber enables a soft feel.
- Rubber Windings – Thin rubber threads wound around a liquid or solid core under tension enhance speed and feel.
- Rubber Cover – Softer urethane rubber cover compounds improve feel, control, and short-game spin.
Manufacturers carefully construct each rubber component to meet desired compression, launch, spin, and feel goals.
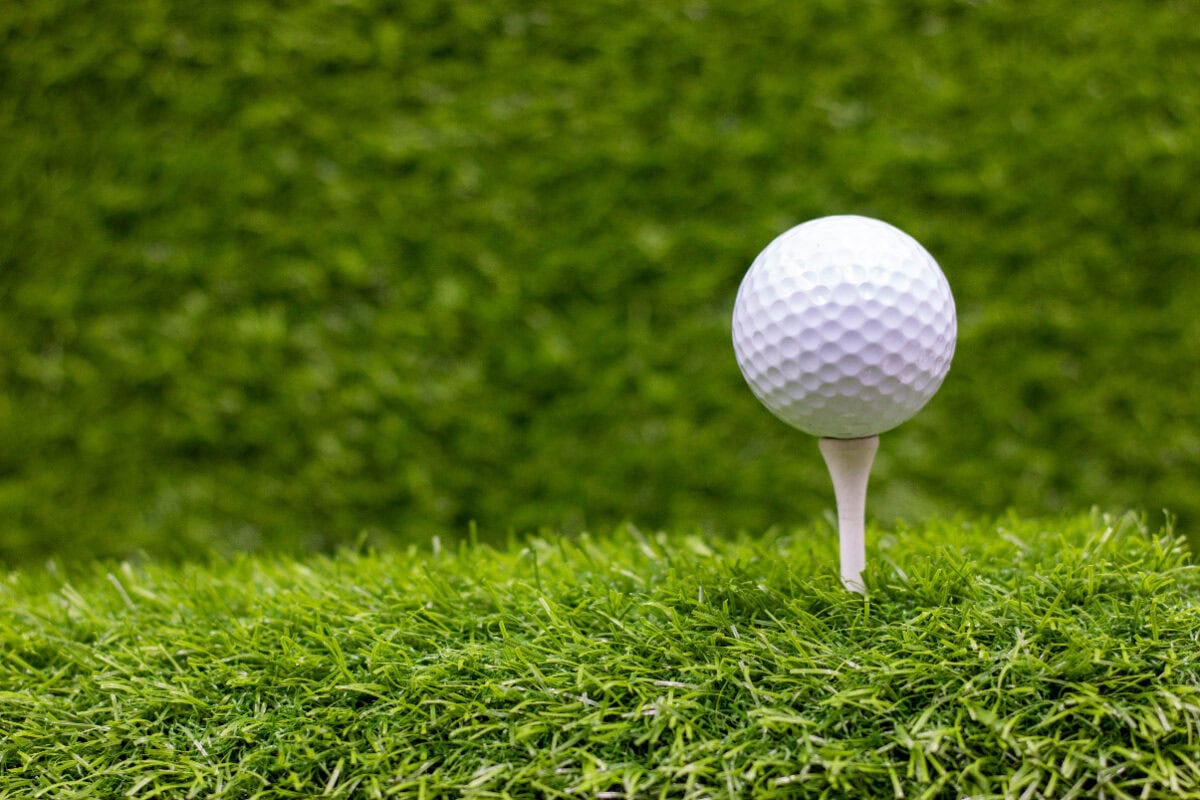
Why Rubber Outperforms Other Materials
Companies have experimented with synthetic polymer and composite cores and covers, but none match pure rubber’s advantages:
- Consistency – Rubber delivers uniform performance not temperature dependent like plastics.
- Feel – Rubber compounds can be fine-tuned for desired softness and response. Synthetics feel firm and “clicky”.
- Workability – Urethane rubber covers in tour balls allow shot shaping and finesse impossible with plastic.
- Durability – Rubber withstands compression force much better than rigid plastics prone to shearing.
These innate characteristics keep rubber as the chosen material for serious golf ball manufacturers.
Rubber Improves With Technology
While rubber itself provides benefits, new processing methods and formulations better unlock its potential:
- Cis-Isoprene – Synthetic cis-isoprene rubber matches and exceeds natural gum rubber grades.
- Metallocene – This specialized catalyst allows superior control of polymerization for precision tuning.
- Cryogenic Milling – Cooling rubber during processing maintains purity and resilience.
- Nanocomposite Fillers – Particles like clay, graphene, and silica enhance durability when added.
Technological refinements will only expand rubber’s capabilities in optimizing future golf ball designs.
Examples of Leading Golf Ball Rubber Innovations
Manufacturers use proprietary rubber compounds and constructions to differentiate their models:
- Titleist FastCore – Formulated rubber core boosts compression for extreme velocity.
- Callaway Graphene Dual SoftFast Core – Graphene-infused rubber maximizes energy transfer.
- TaylorMade React – Rubber incorporating metal-oxide particles increases resilience.
- Srixon Energetic Gradient Growth Core – Precision gradations between rubber layers tunes energetic performance.
- Bridgestone Gradational Compression – Unique vulcanization optimizes each rubber layer’s function.
Through both formulations and layering methods, companies push rubber’s possibilities.
The Future With Rubber Golf Balls
Given its continued superiority in critical performance areas from feel to resilience, expect rubber to maintain its indispensible role as golf ball technology progresses.
With nanoengineering breakthroughs and computational material design techniques, we’re still just scratching the surface of what rubber science can deliver in optimizing golf ball performance.
Advances allowing companies like Titleist and Callaway to microtune each material layer will open new precision frontiers.
While new materials like graphene and metal foams show promise, none match traditional rubber’s broad combination of elasticity, fine-tunable feel, and impact responsiveness.
Refined and enhanced rubber compounds will continue driving future leaps in speed, spin, feel, and control.
So whether sliced into thin windings or foamed into futuristic metallic cores, rubber remains the true heart of the modern golf ball.
With continued research and technology dedicating to unlocking its full potential, rubber will keep golf balls rolling far into the future.